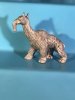
The US Army required a lot of supply in the Civil War; hardtack buiscuit, Whole Bean Coffee, Bacon, Remington Ammunition and Firing Caps, not to mention Springfield Muskets, Kepis, Coats, blankets, shoes, socks, medicines, tools... The US Army six-mule wagon of the Civil War could carry 2,800 pounds of goods and travelled at the rate of 2.5 mph. Each regiment was allotted six wagons, managed by the quartermaster officer, with inventories & load plans for each.
Each regiment needed 6 wagons! and with 4-6 regiments per Brigade, 2-4 Brigades per Division, anywhere from 2-6 Divisions per Corps and several corps per "Army" ie. Army of the Cumberland, or Army of the Potomac... the need for thousands of mules and wagons, including some just to feed the mules and carry parts for the other wagons, skyrocketed astronomically during the war.
The Studebaker Brothers ran a forge and wainwright buissness in Pennsylvania, they'd developed a fine, inexpensive farm wagon and managed to win government contracts to fill the need with their sturdy, handy sized, wagons. The Government General Service Supply Wagon.
so I wanted my Civil War armies to be properly cared for, and this means I need mules and wagons. I COULD buy wagons, but I'm cheap and I wanted to make my own. so I set out to find some references and build a model to make molds from.
anyhow, with some sketched up plans I set to work with scraps of matteboard, and bits of wood....mostly craft sticks and corndog sticks, some wooden beads, and skewers... my trusty xacto, bits of wire and lots of super glue. I knocked together a pretty ok maquette except the wheels are bad, very difficult to arrange the spokes correctly without a proper jig or a lathe. I set it up so it has a hinged back gate, the front wheels properly pivot, and the mules can be attached with a wire harness and bit of jewlers chain. After a bit more delay I pulled the thing apart into pieces. and set about making cornstarch/silicone molds of everything.
That's where I ran into issues. the molds don't work well at all. I haven't gotten a clean cast of any of my parts. there are two major issues. the molds don't fill correctly, the sides are large but thin and the air doesn't vent fast enough so I get big holes in the sides and bottom pieces. the wheels don't fill well either, which is a common problem when casting spoked wheels by the drop pour method, the usual fix is to spin cast these things...but that takes a spin caster. An old solution is to use a coffee can on a chain, pack the mold in sand in the can, pour the metal into the mold and quickly swing the whole thing like a Baeleric Slinger. but I haven't been able to try that out yet. the best fix is going to be re making the molds so they have large resevoirs of hot metal to increase the pressure behind the pour gate, and to run extra sprue, to help keep the mold cavity hot near the distal ends. this is tricky because you can't run these sprues over the vents... I've been racking my brains to plot out the exact best arrangement of vents, sprues, resevoirs, and actual model cavity...
so it's a stalled project. one that I think will be AMAZING if I ever finish it.